In this article you will learn comprehensively how you can achieve so called “Net Zero Printing Waste”, from now on abbreviated to it’s shortened sign-based symbol: Δ°Pw (pronounced ‘DeeZeePaw’)
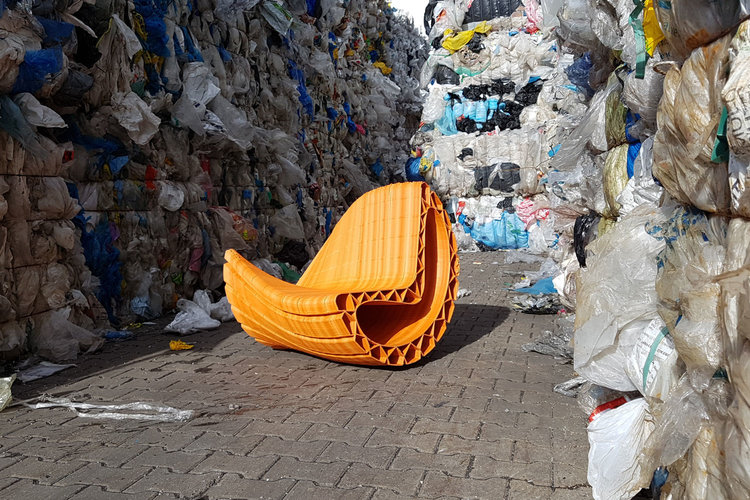
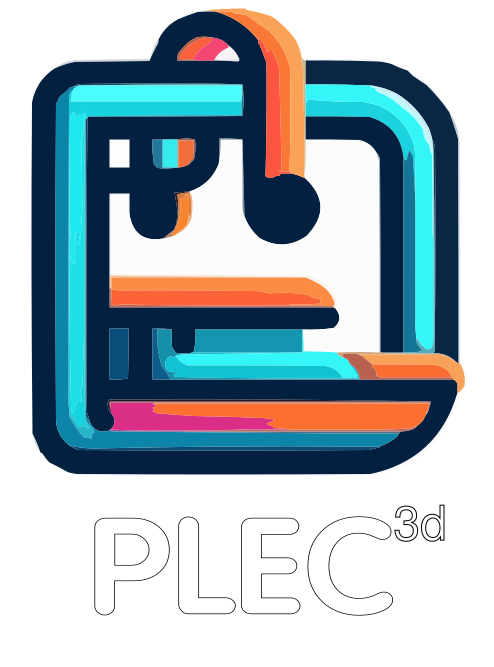
WASTE NO WASTE, USE YOUR GREY PASTE
The problem with 3D printing and it’s sustainability can be subdivided into two categories:
– A) plastics recycling difficulty and
– B) slow degradation of plastics in general.
These two are of course linked together; the long lifespan of plastics make the need for recycling very important.
You could because of these two interlinked problems basically think of two main ways to solve 3D printing sustainability:
- 1 – use of degradable plastics, not like PLA which degrades in many centuries but like f.e. PHA/PHB (biomicrobial plastics) which degrades within a few years, and faster even in composters.
- 2 – recycling of your plastic, which is for all non-degradable plastics a must to avoid wasteland situations. This can be done either by sending it to a recycling facility or using an home-owned recycling machine.
Of course which option will suit you best depends totally on your own use-case.
As for the first option; degradable plastics:
All normally used printing plastics, even ones marketed as biodegradable and plant-based; like PLA, are completely not biodegradable. They are in theory degradable on industrial (read high temp, really energy wasteful) landfills, but those only exist on paper and it would still take decades and have no financial advantage to the organising party. Basically PLA is completely not well degradable, it takes centuries to degrade PLA in nature.
However real biodegradable plastics are sold already for quite some years. A plastic polymer named PHA and PHB are microbial made plastics that degrade in a few years in nature.
For a lot of use-cases like prototypes or functional (household) parts, ones that don’t come into contact with water, they are great, the improved specs are a good bonus: they have better stiffness and better bending ability (compared to PLA/ABS/PETG).
On top of that they come from green(er) sources; no oil or questionable soil-depleting cheaper agriculture are used for their production.
PHA/PHB are sourced by feeding microorganisms, bacteria, with waste material and sugars and having them create polymers as side product.
To my knowledge there are a handful brands selling PHA/PHB, in the next paragraph we give a small list of some relatively good available ones.
Some noteworthy filaments for bio-degradation (degradation within years in nature), are:
– Filamentum NonOilen — pretty easy to print, may warp a little if printed hotter than 200°C, so print a bit slower. food-safe, favorite for functional parts. only in natural color.
– Colorfabb allPHA — pretty sticky and tends to clog sometimes, not too expensive. available in natural, black and white.
– Colorfabb PHA/PLA — improved specs compared to normal PLA and degrades quicker because of PHA content. budget-friendly and available in natural, black and white.
However, for circularity, it is of course also an option to use recycled filament, which is often as good or sometimes even better than so called ‘virgin’ filament. You can find it by putting a small ‘r’ in front of the filament type, like rPLA for PLA. You can find lots of options from lots of vendors.
What is a new and very smart solution that really cuts on two sides is the use of waste fishing nets and carpets to make nylon. Nylon, great for printing sturdy heat-resistant stuff, great for for example gears and mechanical parts, is a bit harder to print, it warps quite easily so needs a very hot bed and preferably a closed chamber (non-heated). Noteworthy options for it are:
– Filamentum Porthcurno and Orca – rPA and rPACF carbon fiber filament
– Reflow rPPGF and rPACF – well priced and really super great tensile strength (8800+MPa)
As for the second option; recycling printed plastics:
Basically there is an intrinsic feature of plastics to be thermally reshape-able into new shapes, hence their name as you might have guessed, so theoretically plastics could be recycled hundreds of times even.
There are still two problems, the first is that your plastics won’t be of much use when intermixed with different types as they will not be printable anymore at a static temperature if mixed. You can print our modular plastic and keep types sorted separately easily from now on. Then, the next important thing is that to melt the plastics you will need to crunch the printed parts to small granules and ideally even create new filament straw, which is quite heavy work to do. You can buy or build your own machine for this, for example the Artme3D DIY kits (around 700) or the more professional grade assembled machines, like from 3devo.
However, for that step there is a much simpler solution nowadays; using a recycling service; a company that does the hard work for you, and they often give you some sort of bonus back, like cheap filament or even free sometimes, which is nice next to your good use of grey matter:)
So thankfully a company called Prusa published a nice map to find a location near your place, see below. Pay attention to click “3D printing waste recycling” in the top left under “Available services” to filter to recycling services!
Prusa published a small overview on how the map was made, see here.
So another interesting question you may have is how big the problem is with 3D printed plastics waste. There is research done on this, but that research seems to be greatly based on educated guesses.
If you are searching for the amounts of waste generated by 3D printing worldwide; there is little information available but the following page gives some info for the UK:
How Much Plastic Waste does 3D Printing Really Generate? (filamentive.com)
But what becomes very clear when you delve deeper into the plastics issue is that we really need to quickly transitiont degradable plastics as base for almost everything we produce, only perhaps some nylon for longevity requiring products that are provably going to be used long.
And, the source of the plastics should not come from either oil as it is enormously toxic to living organisms, or from sources that require a lot of land and should be used for food production, as they are inefficient for plastics, requiring relatively much resources to be grown and land that should be used for nature reforesting.
A first great new venture into biodegradable plastics is found in the use of PHA made by bacteria from sugars, which can be resourced from leftover fruits or food, as replacement for PLA or PEF, made from waste material, as replacement for PET. This article explains a lot more about these (A look at biobased alternatives to PET bottles | Article | Packaging Europe).
Another great idea for getting the substrate to make plastics at scale quick would be the use of algae, which grow fast and produce great sources for plastics.
This product can be bought in reality already!!
Don’t wait any longer, get your algae flip flops right now! : ECOALF – Sustainable and Recycled Clothing
And share/ buy them for others!
(P.S> dispose of your old ones responsibly; throw them away in the garbage, at least they should not end up in the oceans, while your new ones won’t harm if they end up there!)
An important problem also with the way plastics dealt with today is that they end up in landfills and/or at some point get transported to poor countries as solution to the disposal. This is a global problem that richer countries should together make an end to by cooperating and chipping in the, relatively small amount of money required to do disposal differently. This movie shows the effects in a poor country:
More interesting links about creating biodegradable filaments:
BIO-PLASTICS EUROPE (bioplasticseurope.eu)
CLIFF Project (https://cliffproject.eu)
We need to now get into using the alternatives and move the productive industry to the future by buying the new sustainable products instead, even when it is a new company with new looks, and not our old accustomed one, because it helps good instead of just the old bad!
If you would like to find a local sustainable shop to buy sustainable products, you can make use of certified companies that are so called B-corps, click to find one in your area: –>here
(P.S> Try the search bar in the top to enter the area of interest you search for)
There are also industrial initiatives taking up the recycling task of plastics, but they only try to solve industrial plastic recycling. An example
Then, last but not least, one last hint for reducing your 3D printing waste:
Use PLEC³ᵈ’s solutions, for the moment that is Yaint; the non-planar printing app that lets you break away from using any support on your prints, all the while increasing the strength and smoothness of your prints!!
And Iris, our slicer also contains tool clustering to minimize tool changes and thus purge-waste and MMU pre-loading, to load in advance relatively to the amount of filament between MMU and nozzle outlet. Reduce your waste to zero with these features right now by starting using them, Iris is completely free to use, Yaint only costs one cup of (pretty cheap) coffee at $2/m.
In the very near future PLEC³ᵈ’s new color printing kit will become available that will allow full-color totally purge-free! (using Arara, full-color toolhead, and Harpy, smart MMU). Subscribe now to PLEC³ᵈ and start using Yaint and be updated on the new members of the family as soon as they come out!
Have fun printing Δ°Pw (DeeZeePaw) on your printer!!
Share about it online!